Measurement of energy savings
DATE:2024-12-12
Read:
SHARE:
In this paper, on the basis of analyzing the flue gas waste heat recovery system and the energy balance and conversion relationship of each link, the method of indirectly measuring the energy saving of the whole waste heat recovery system and its boiler combustion air preheating by using temperature sensors, heat meters and other conventional instruments is proposed, and the results of the measurements before and after the use of the flue gas waste heat recovery of the water vapor heat-carrying boiler are given by the example of the Shandong Linyi Hengli Cogeneration Power Plant. The data analysis shows that for a boiler with an evaporation capacity of 176.90 t/h, the total energy saving of the whole flue gas waste heat recovery system is 10.86 MW, accounting for 8.46% of the boiler's heat production, of which the boiler heating combustion air through the preheating and humidification of the boiler's inlet air saves 1.73 MW of energy, which accounts for 16% of the total amount of waste heat recovery. This measurement method provides technical support for online real-time monitoring of energy saving for the scale application of flue gas waste heat recovery system of water vapor heat-carrying boiler.
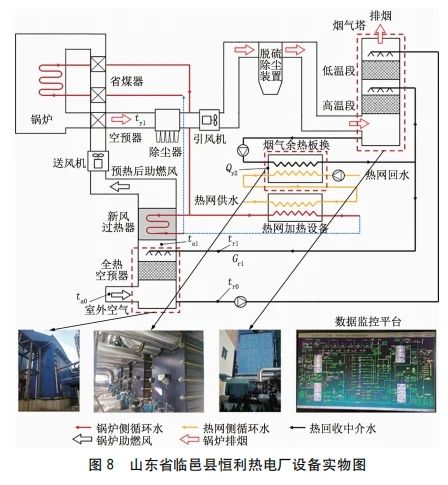
Boilers are accompanied by a large amount of high-temperature flue gas emissions during the heat production process, and at the same time release a large amount of CO2 and other greenhouse gases. Flue gas waste heat recovery can not only reduce the heat loss of the boiler, but also reduce fuel consumption and greenhouse gases and other pollutants, and improve the thermal efficiency of the boiler, therefore, the development of flue gas waste heat recovery technology is an important way to help the realization of the “dual-carbon” strategic objectives. Existing flue gas waste heat recovery system mainly includes three categories: the first is the use of inter-wall heat exchanger to realize the flue gas waste heat recovery, that is, the use of low-temperature economizer or energy saver, etc., in the boiler outlet flue with the addition of heat exchangers such as tube type structure, recovery of flue gas waste heat and heating boiler feed water or heating return water. This way of simple form, the total cost is relatively low, to a certain extent, can realize the depth of flue gas waste heat recovery, but its shortcomings are the waste heat recovery rate is low, the need for heat exchangers for anti-corrosion treatment. The second category is the use of absorption heat pump flue gas waste heat recovery technology. Absorption heat pumps are used to recover flue gas waste heat and heat network return water, flue gas temperature can be significantly reduced to about 30 ℃, the amount of waste heat recovery equivalent to 8% to 15% of the boiler's heat production, so the depth of heat recovery can be realized. However, absorption heat pumps need to consume steam and other high-grade heat source drive, and because the flue gas will produce a large number of acidic condensate, the need to use corrosion-resistant heat exchangers, equipment investment is relatively high. The third category is based on the air - flue gas total heat exchange recovery technology, through the humidification of combustion air to increase the dew point temperature of the flue gas, in front of the chimney at the flue to recover the condensation heat of the flue gas. The system structure of this method is simple, no additional driving heat source is needed, and the investment cost is low, so it has a good application prospect. In recent years, the water vapor heat-carrying boiler flue gas waste heat recovery technology jointly developed by Tsinghua University and Beijing Tsinghua University Tiangong Energy Technology Research Institute is a typical air-flue gas total heat exchange to realize the deep recovery of flue gas waste heat, which has been popularized and applied on a large scale, and its technical principle is shown in Figure 1. Calculation and analysis show that this technical solution can deeply recover the flue gas waste heat equivalent to 8% to 15% of the boiler heat production, and the unit waste heat investment can be reduced by more than 15% to 20%. However, in the actual engineering application, due to the program to improve the boiler combustion air inlet temperature and moisture content, caused by the boiler combustion process of heat transfer, flue gas composition and flow rate and other parameters of the change, which further led to the boiler air intake is difficult to accurately measure; and part of the boiler flue gas waste heat through the plate heat exchanger (hereinafter referred to as plate heat exchanger) is used to heat heat the heat network back to the water and process water, and the other part is used for the boiler The other part is used to heat and humidify the incoming air of the boiler, so the process of waste heat recovery and utilization is complicated, and it is difficult and controversial to measure the energy saving by traditional methods. Therefore, it is necessary to establish a set of accurate and applicable energy-saving measurement methods for water vapor heat-carrying boiler flue gas waste heat recovery technology in order to accurately measure its energy-saving effect and evaluate its benefits.
Back
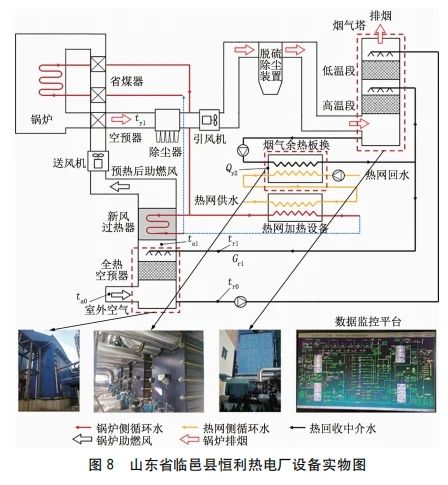
Boilers are accompanied by a large amount of high-temperature flue gas emissions during the heat production process, and at the same time release a large amount of CO2 and other greenhouse gases. Flue gas waste heat recovery can not only reduce the heat loss of the boiler, but also reduce fuel consumption and greenhouse gases and other pollutants, and improve the thermal efficiency of the boiler, therefore, the development of flue gas waste heat recovery technology is an important way to help the realization of the “dual-carbon” strategic objectives. Existing flue gas waste heat recovery system mainly includes three categories: the first is the use of inter-wall heat exchanger to realize the flue gas waste heat recovery, that is, the use of low-temperature economizer or energy saver, etc., in the boiler outlet flue with the addition of heat exchangers such as tube type structure, recovery of flue gas waste heat and heating boiler feed water or heating return water. This way of simple form, the total cost is relatively low, to a certain extent, can realize the depth of flue gas waste heat recovery, but its shortcomings are the waste heat recovery rate is low, the need for heat exchangers for anti-corrosion treatment. The second category is the use of absorption heat pump flue gas waste heat recovery technology. Absorption heat pumps are used to recover flue gas waste heat and heat network return water, flue gas temperature can be significantly reduced to about 30 ℃, the amount of waste heat recovery equivalent to 8% to 15% of the boiler's heat production, so the depth of heat recovery can be realized. However, absorption heat pumps need to consume steam and other high-grade heat source drive, and because the flue gas will produce a large number of acidic condensate, the need to use corrosion-resistant heat exchangers, equipment investment is relatively high. The third category is based on the air - flue gas total heat exchange recovery technology, through the humidification of combustion air to increase the dew point temperature of the flue gas, in front of the chimney at the flue to recover the condensation heat of the flue gas. The system structure of this method is simple, no additional driving heat source is needed, and the investment cost is low, so it has a good application prospect. In recent years, the water vapor heat-carrying boiler flue gas waste heat recovery technology jointly developed by Tsinghua University and Beijing Tsinghua University Tiangong Energy Technology Research Institute is a typical air-flue gas total heat exchange to realize the deep recovery of flue gas waste heat, which has been popularized and applied on a large scale, and its technical principle is shown in Figure 1. Calculation and analysis show that this technical solution can deeply recover the flue gas waste heat equivalent to 8% to 15% of the boiler heat production, and the unit waste heat investment can be reduced by more than 15% to 20%. However, in the actual engineering application, due to the program to improve the boiler combustion air inlet temperature and moisture content, caused by the boiler combustion process of heat transfer, flue gas composition and flow rate and other parameters of the change, which further led to the boiler air intake is difficult to accurately measure; and part of the boiler flue gas waste heat through the plate heat exchanger (hereinafter referred to as plate heat exchanger) is used to heat heat the heat network back to the water and process water, and the other part is used for the boiler The other part is used to heat and humidify the incoming air of the boiler, so the process of waste heat recovery and utilization is complicated, and it is difficult and controversial to measure the energy saving by traditional methods. Therefore, it is necessary to establish a set of accurate and applicable energy-saving measurement methods for water vapor heat-carrying boiler flue gas waste heat recovery technology in order to accurately measure its energy-saving effect and evaluate its benefits.